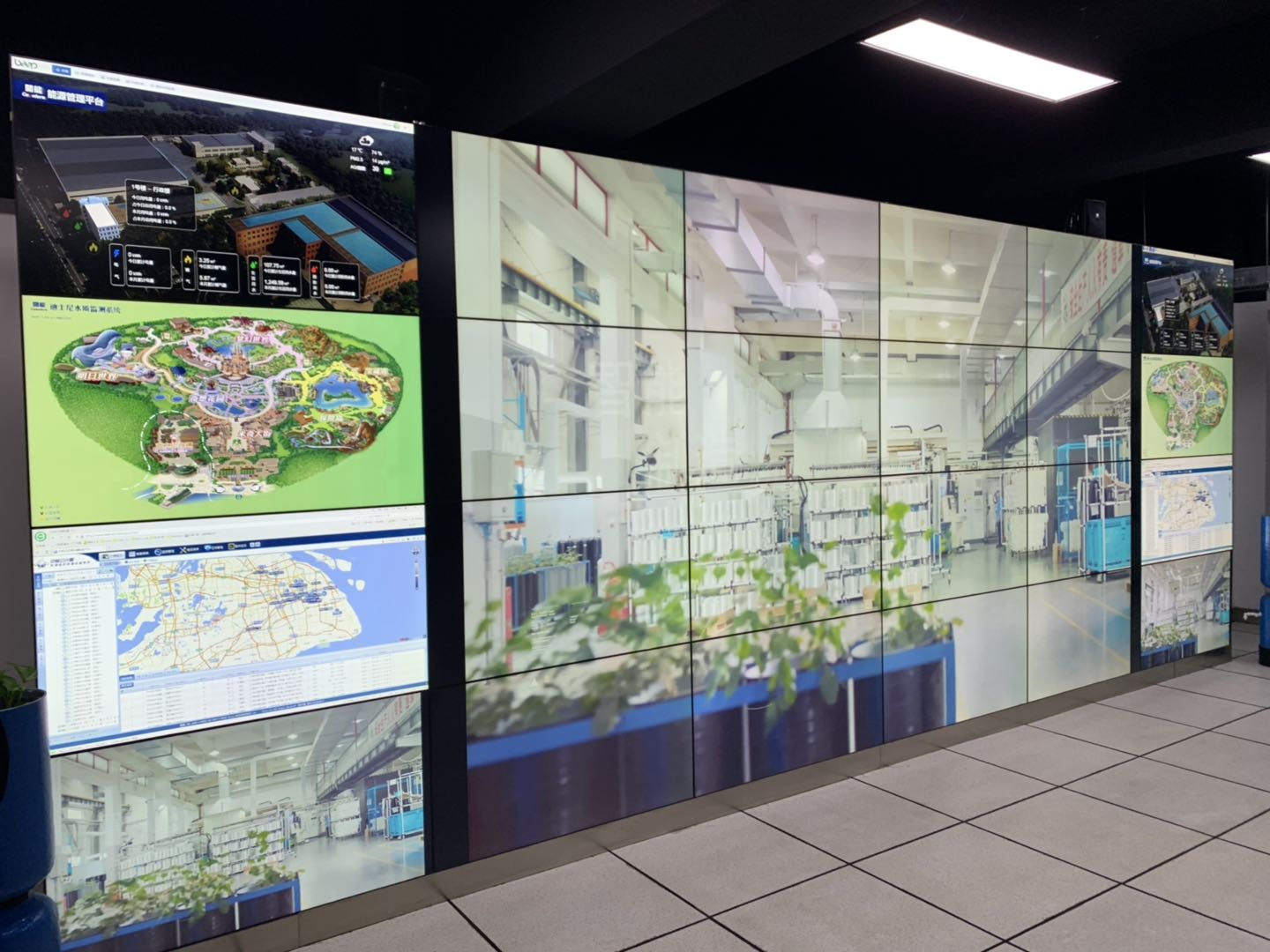
突如其來的疫情给经济社会发展带来巨大挑战,而以无人工厂、不见面生产等为代表的一批在线新经济,正成为“上海制造”对冲疫情影响的重要工具。上海市经信委相关负责人表示,上海制造业已基本完成从自动化到数字化的转型,已初步具备无人工厂建设条件。
伴随着新一代技术的演进,在这些“无人工厂”里,智能制造取代了部分岗位,线上的数字管理系统取代了纸质的记录,同时也催生出了许多更有创造力的岗位,迎来了发展的新契机。
车间之变:
全自动线减少了人员依赖
复工一周后产能恢复至90%
车间是制造业最基本的单元,同样也是智能改造升级的窗口。通过远程运行维护、大数据、人工智能等综合手段,沪上老牌净水品牌开能的制造车间变身一座24小时运转,不需要多人值守的“无人工厂”。经过多年探索,如今开能工厂的自动化率达到了70%。
开能健康副董事长翟亚明说道,任何事物都有两面,这次疫情对于远程、移动、智慧方面的产业和应用是契机。“如果还像过去传统的靠人工操作,不仅出错率高,万一有人感染,整个班组都要被隔离,这对现场生产带来的冲击就非常大。”
2月10日,开能成为上海市制造行业里最早复工的一批企业,复工一周后,工厂人员到岗率达到50%,而产能已经能够恢复到90%。
在记者1个多小时的走访过程中,7个生产车间,全程都看不到几名工人,而在原材料车间作业的工人也不需要接触例如活性炭等化学物质。原材料经由一个巨大“铁塔”输出,被装进密封储罐里,通过运输链送至下一道生产工序,标准化生产避免了原料厂与工人直接接触,也保证了工人的安全以及作业环境的整洁规范。
“以核心部件玻璃钢桶压力容器制造车间为例,原先一天制造1000个桶需要35名员工,引进全自动化产线后,现在只需7名员工,在产能不变的前提下效率提升了80%,整个车间增加的9台机器人替代了三十名员工的生产力。”翟亚明说。
他补充,随着商业模式的变化,以及互联网的发展,工厂面临的生产和物流需求也愈加复杂。不同于成熟行业如汽车或新兴行业如电子商务,开能拥有大量的定制化产品,而且集销售、生产、制造于一体,且客户群体较复杂。因此,工厂分别上线了一期和二期智能仓储。
在现场,记者发现了该工厂智能仓储的独特之处。首先,不同于其他制造型企业将原料、半成品、成品分开保管的模式,开能健康将原料、半成品、成品以及模具共同存储,增加了仓储操作的复杂度,所以适应性非常广。
翟亚明介绍,“全自动立库,原材料直接到车间,成品直接入库。这样一来减少了大部分的人员依赖。而我们的信息系统,减少了大部分的调度和支持人员。”
员工之变:
为员工创造更多价值
吸引更多年轻一代选择制造业
智能制造对于“上海制造”的改变,同样发生在一线工人的身上。相比较传统机械、重复的劳动内容,现如今车间里的工人常常看不到他们爬高举重的忙碌状态,取而代之的是一头扎在机器里。“把生产经验‘教’给机器”,是智能工厂工人们的共同特征。
开能改造智能车间之初,也在思考如何为自己的员工创造更多价值。“现实的问题是,我们需要吸引年轻人来加入制造这个行业,用什么方式?那就用年轻人喜欢的方式,为他们创造更多工作价值。”开能的方法是,通过帮助员工不断提升自我技能。例如通过产业升级,以帮助员工从单一、繁重的生产操作中解放出来,然后升级成为管控自动化生产的人才,实现收入、技能的双提升。
人因岗位而变,岗位同样因人而变。当智能制造取代了一部分枯燥且没有创造性的岗位时,也催生出许多新的岗位。
开能目前共有两百多名一线工人,在车间升级同时,他们也在技能提升了上得到了新的机会。例如开能精益生产项目,就是鼓励工人利用自身生产经验,对自动化生产线进行改造。比如吹塑车间和缠绕车间通过精益生产和自动化改造,将吹塑与车口岗位合并,实现了单件流作业,不仅节约了3名车工及2台车床,同时也减少了等待时间,实现效率的较大提升。
产业之变:
智能化改造企业
提升生产效率、降低运营成本
无人生产,智能制造是传统制造业转型升级的重要方向之一,整体来看,上海已有一定基础。
数据显示,2019年,上海智能制造产业规模超900亿元,规模和能级位居国内第一梯队,在《2019年世界智能制造中心城市潜力榜》上,上海排名世界第二。上海市经信委相关负责人表示,上海制造业已基本完成从自动化到数字化的转型,已初步具备无人工厂建设条件。
目前,上海在汽车、高端装备等重点领域已建成国家级智能工厂14个、市级智能工厂80个,推动规模以上企业实施智能化转型500余家,企业平均生产效率提升50%以上,最高提高3.8倍以上,运营成本平均降低30%左右。通过智能化改造打造无人工厂、黑灯工厂,将使越来越多的企业插上翅膀,重新焕发活力。