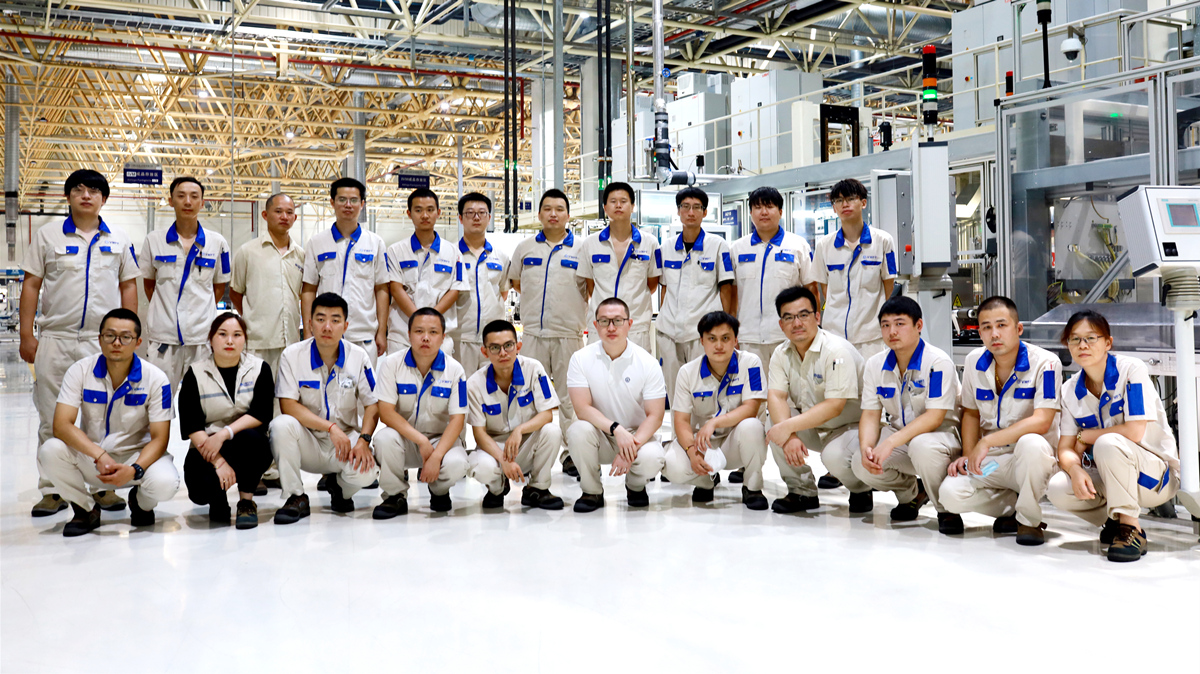
来自上海大众动力总成有限公司(以下简称“大众动力总成”)制造部的罩壳模块生产班组享誉业内,它是公认的大众集团在中国区最好、最优的一条生产线班组。班组现有成员73位,秉持着精益求精的工匠精神,一群平均年龄30岁的年轻人在数年中为企业发展取得了累累硕果。
攻破国际技术壁垒
在罩壳模块生产班组“大事记”上,仅用8个月时间攻破德国大众EA211凸轮技术垄断壁垒是全体成员的一次高光时刻。
2014年,响应集团降本增效的号召,零件国产化势在必行,大众动力总成主导开展“凸轮国产化攻关项目”。当该零部件进入调试生产阶段时,加工过程中一个关键参数指数始终达不到图纸设定的要求,攻关进程一度受阻。以罩壳模块生产班组长、上汽工匠徐田为首的核心成员组成团队,与设备供应商联系取得一手资料,经过多次现场模拟反复论证,改进了磨削程序并进一步优化了喷淋方式,最终顺利解决了这个项目上的“拦路虎”。
之后,为了更好应对批量国产凸轮的生产,班组成员针对国产件的加工特点及参数每周做定期数据采集、分析、经验分享交流,由班组长首先自己掌握设备特点在传教给班组负责工位的操作工,如同大雁领头带领一群雁子飞翔一样,带领着团队整体前进。
技术改进创新不断
在大众动力总成内,罩壳模块生产班组也是一个兼具知识、技能、创新的团队,各式技改、发明不断。
缸盖罩壳成品下线工位原先使用纯手动进行零件防锈,生产环节完全敞开式,当油雾挥发到空气中,容易造成操作工职业健康危害。为了改善员工作业环境,减轻劳动负荷以及降低质量隐患实际问题,生产线成立了项目攻关小组进行全面的研究与分析,改善优化原先的工位设备,保证该工位产品下线涂油合格率、降低员工劳动负荷,消除了环境污染,保障员工身体健康。
(罩壳模块生产班组长徐田(中间)正为组员开展零件装夹教学。受访对象供图)
从2016至2022年间,团队开展持续改进和合理化项目236项,共完成设备优化项目138项,共节约成本1800余万元。其中26项在全球大众生产专家会议上被作为优秀案例推广,获得国内外广泛认可。
完善成熟的育人机制
班组先后培养了高级工15人、高级技师3人、技师1人、中级工程师1人,公司未来工匠12人,并向大众全球生产专家团队输送专家12人。而炼就这样一个技术创新班组,成熟且完善的育人机制是核心“驱动力”。
班组首创生产维修“双轨”工作法,有效提升维修工以及操作工的各项通用能力,彼此联合解决设备重复性故障,提高生产效率;每月进行案例分享会,通过彼此经验的交流分享,不断促进班组降本增效;以透明质量文化建设理念为先导,创新性搭建跨部门联动平台,集结各部门、各模块精英共同致力于质量问题的及时解决,通过各部门之间的资源共享,打开解决问题的快速渠道。而在顺应汽车行业深度调整,新技术加速更新迭代的当下,班组以海鸥工作室为平台,培育数字化人才,运营3D打印、虚拟仿真等技术,提高生产效率。
(头图:上海大众动力总成有限公司制造部罩壳模块生产班组部分成员合影。受访对象供图)